by:
How to Reduce Manufacturing Waste
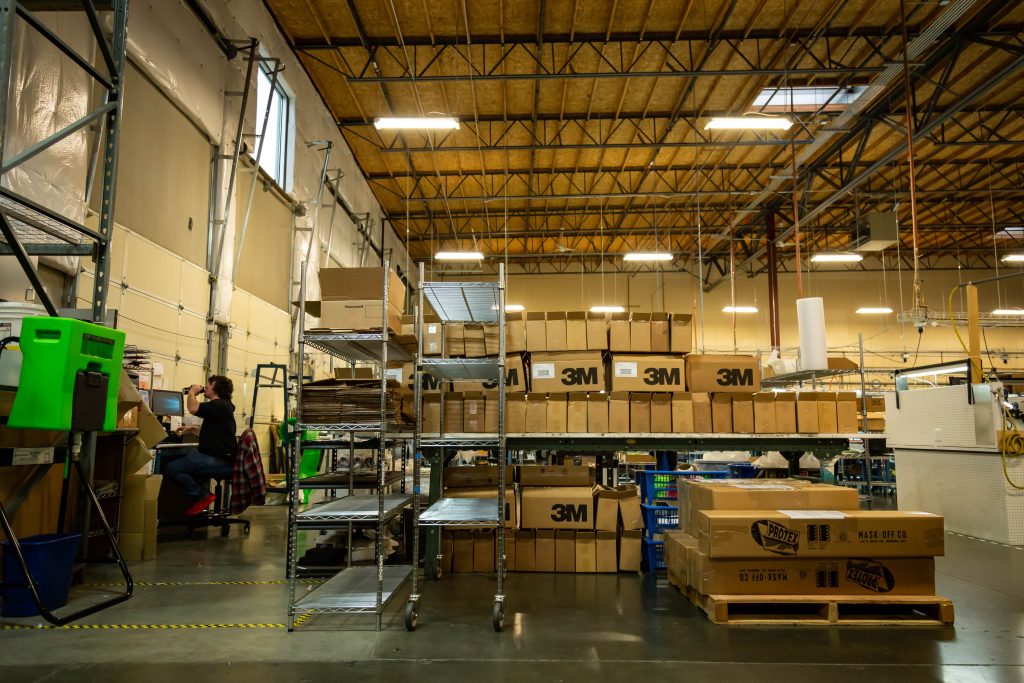
In search of greater competitiveness, waste reduction is a critical factor. Identifying problems is the first step to eliminating or reducing them.
There are several ways to understand what waste is. For some it is any inefficiency incurred in the use of equipment, material, labor or capital. It refers both to wasted material and to the execution of unnecessary work. Obviously, this causes additional costs and does not add value to the product. Consequently, the foundation of the concept of waste is related to the fact of originating costs and not generating value.
Waste is an inefficiency that reduces competitiveness and produces an increase in value over cost. Consequently, waste decreases the value for customers and directly affects lower profits.
How to Reduce Waste in Manufacturing?
There are several philosophies that allow us to reduce waste and reduce our costs. One of them is Lean Manufacturing, which points directly to the identification and elimination of activities that do not add value in all the processes in which a company is involved: design, production, the supply chain and the relationship with customers.
For Lean Manufacturing, any element within the indicated processes that adds cost without adding value to the product is considered waste. In this sense, waste costs money, takes time to make the product and deliver it in a timely manner, consumes more resources, decreases productivity, increases costs without generating value or profit, and deteriorates the company’s competitiveness.
Typical Wastes Generated by the Manufacturing Industry
Lean Manufacturing classifies waste according to its origin. This source of waste can be found in material manufacturing, training, design, material supply, or planning.
Waste classification:
Now we will see the types of waste. Knowledge of this typology helps to identify when the following occur:
Overproduction: a quantity greater than required or ahead of time is produced. This implies the waste of materials, hours of work and use of equipment. Causes inventories and storage of unfinished products.
Waiting times are the dead times incurred due to lack of synchronization between work teams, lack or excess of materials, poorly balanced lines, poor production programming, and poor maintenance of machinery or equipment. A bottleneck.
Transport: there is an unnecessary or poorly planned movement of material, even in the case of a supplier. It also refers to excessive cargo handling, the use of inadequate equipment, excessive travel of materials, temporary storage of material. Thus, hours of work, energy, space and material are lost. The unnecessary movement of personnel and information is also considered waste.
Processing: Unnecessary work is done that is not a normal part of a process and for which the customer is not willing to pay. Here they are: unnecessary checks, inspections, unnecessary signatures, unnecessary paperwork, etc. These actions usually occur due to poor planning, programming and production control or due to lack of application of technology.
Inventory: the accumulation of products or inputs in any part of the process is a “stock” inventory. This generates other forms of waste such as waiting time, maintenance, additional storage space, re-work, material losses (due to deterioration, inadequate conditions, theft, vandalism) and monetary losses due to “sleeping” capital. The inventory is the result of the lack of planning and the lack of knowledge of the quantities required.
Movement: there are cases of unnecessary or inefficient movements made by the staff. It involves the inappropriate use of equipment and ineffective work methods due to lack of previous studies. Unnecessary movement of machinery is also considered here.
Defective production: the final product does not meet the quality requirements, which could lead to re-work, so that producing a good in these cases would have a higher cost that could even exceed the production cost of a good manufactured under normal conditions. It is incurred due to poor design and specification, lack of planning and control, and lack of consistency between design and production.
RELATED BLOG POSTS
Discover Bridgeways’ Capabilities: Delivering Excellence Across Industries
Build Better with Bridgeways: Manufacturing Excellence and Community Impact
The Power of Contract Manufacturing
In today’s fast-paced and competitive business landscape, companies are constantly seeking ways to streamline their operations, reduce costs, and maintain high-quality standards.