by:
JUST-IN-TIME: THE SOLUTION TO IMPROVE MANUFACTURING OPERATIONS
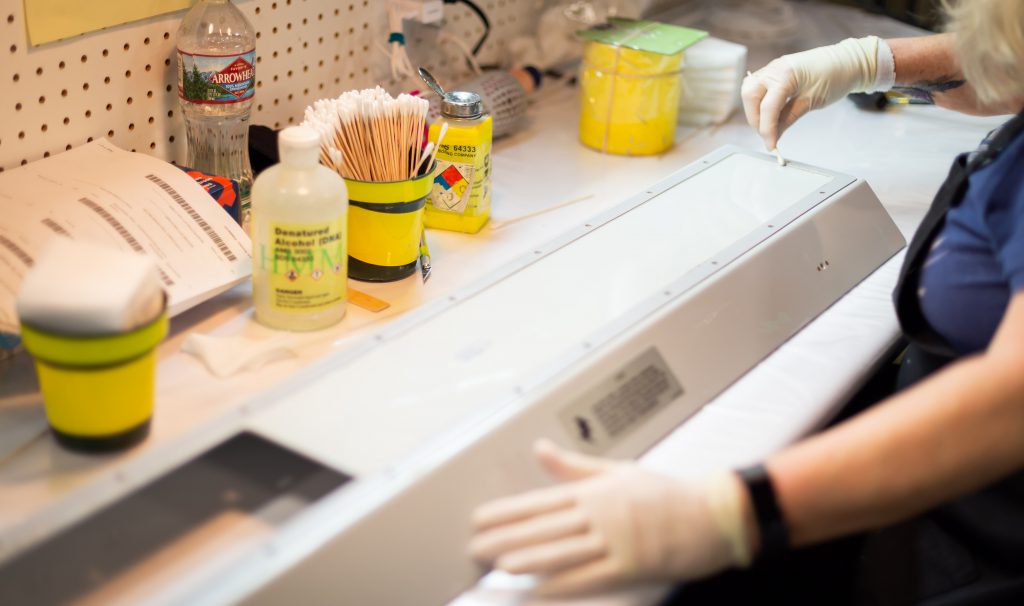
The search for a methodology to improve business production is not a consideration that has arisen recently. In the case of the manufacturing industry, the development of methods to increase productivity is constant, especially with the rise of a more global economy of markets. One of the countries that has presented some of the most contributions toon this topic is Japan. After its defeat in World War II, Japanese industry managed to recover quickly thanks to certain methods they implemented. However, in the 1970s it seemed that the post-war mode of production was running out of steam. For this reason, the Toyota company began to introduce some changes that led to the Just- in- Time system, whose success caused it to spread to the rest of the world.
What is Just-in-Time Manufacturing (JIT)?
Just-In-Time is a system for organizing factory production methods developed in Japan by Taiichi Ohno. This mode of organization was created for Toyota, one of the most important automobile manufacturers of our time. It has now spread outside of Japan and, become very popular in recent decades.
This methodology is intended to optimize the entire production process through the continuous elimination of waste such as that produced by transportation, storage and/or preparations. Its work philosophy is summed up in its name: whether for manufacturing or customer service, both raw materials and products arrive just in time.
At first, this system was only thought to only be tenable in Japan, since it was linked to the cultural, social and philosophical traditions of the country. However, its subsequent expansion showed that, although it represented a great change in the way of producing, the method could be adopted anywhere in the world.
Just- in-Time is an industrial production methodology that aims to eliminate all waste generated during the production process.
The basis of this methodology is perfectly summarized in one of its most classic definitions: ““Just-In-Time is based on having the elements that are needed, in the quantities that are needed, at the moment they are needed.”
In this way, both the necessary materials and the finished products must be available in the right place, at the right time and in the quantities required.
How does the just-in-time production method work?
Very briefly, this system is ultimately designed to deliver the materials to the factories and the products to the customers “Just- in- Time”. For this to be effective, only the necessary resources will be used, both in variety and quantity.
One of the impacts of implementing this methodology is a reduction in the need for storage. That being said, this also means that Just-In-Time requires an extraordinary amount of precise organization.
A good example is to look at Toyota: it receives the materials, assembles the cars and takes them off the production line within a single day. This thereby reduces management costs, reduces inventory review costs and minimizes potential losses that may occur in warehouses.
The Just- in- Time method is based on a simple premise, but it requires the awareness and participation of the entire workforce. In short, it is about complying with the maxim that its name indicates: both the materials and the finished products must be prepared “just- in- time”. This implies that supplies have to arrive at the factory shortly before they are to be used and in the right quantity. Similarly, the product must be made when the customer requires it.
Main Characteristics of JIT
Among the most important characteristics of the Just- in- Time system, the following are the most crucial for successful implementation of the system. can be pointed out:
Cellular manufacturing: To simplify the processes, the first thing is to organize them in such a way that the material flows are simplified. In this way, a particular kind of distribution is usually preferred in which the machines are organized in a U-shape, in order to facilitate faster access by workers.
Multi-skilled workers: The training provided to workers must be incredibly comprehensive. The objective is that they can use any machinery in the factory, with which they will be able to attend to several different functions within the cell at the same time.
On the other hand, it is very common that these workers will also carry out other tasks, from the transport of materials to small repairs.
Pull Production: Unlike the so-called “Push” production systems, Just-in-Time prefers Pull systems. With the latter, production will not start until customers require it.
Elimination of waste: Any type of waste, of materials or time, translates into an increase in the cost of the product and a decrease in quality. One of the main objectives of the Just- iIn- Time method is to eliminate any form of waste. In addition, it aims to simplify the entire manufacturing process as much as possible, making it easier to detect and solve any problems that may appear.
Involve the staff: Another characteristic of this methodology is the effort to get the workers involved in the company. Likewise, it is essential that the relationship with the suppliers is very close.
Part of the strength of this system is that this cooperation extends to design engineers as well. In this way, the necessary changes in designs and improvements to save costs are much easier. The fact that the batches are smaller and the deliveries more frequent, facilitates communication with the suppliers and, therefore, the possibility of correcting any possible error in a much faster time. .
Seek simplicity: In many cases, the simplest approaches can lead to more effective management. It is considered that any system capable of identifying problems ends up being beneficial.
Conclusion
For decades, Bridgeways’ focus is to help our customers grow together, support each other, and seek ideal solutions and budgets without compromising product quality. Through efficient and high quality processes, we encourage clients to innovate and continue to grow their business. Contact us today and get a free quote!
RELATED BLOG POSTS
Discover Bridgeways’ Capabilities: Delivering Excellence Across Industries
Build Better with Bridgeways: Manufacturing Excellence and Community Impact
The Power of Contract Manufacturing
In today’s fast-paced and competitive business landscape, companies are constantly seeking ways to streamline their operations, reduce costs, and maintain high-quality standards.