by:
Modern technologies impacting manufacturers
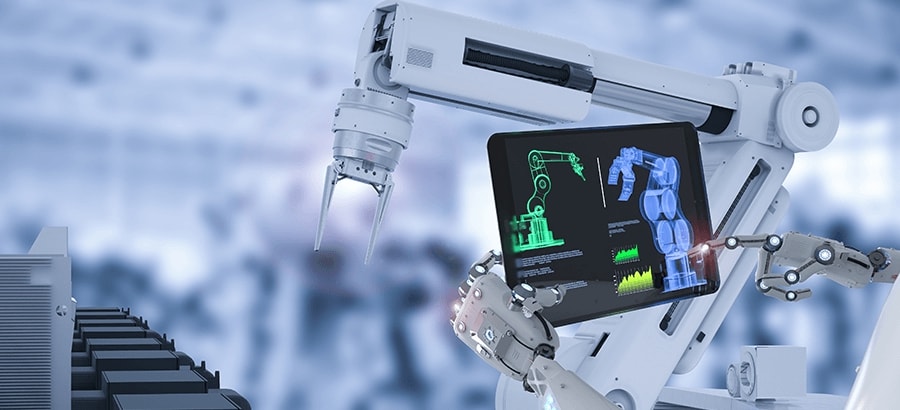
Imagine assembly lines that are never affected by unplanned downtime, maintenance work that is scheduled at an exact point in time, and spare parts that arrive even before they are needed. No more warning lights that flash only after an error has occurred or a part has exceeded its life cycle.
These and other benefits are offered by the establishment of intelligent manufacturing or industrial internet, which began in Germany with the name of industry 4.0. This refers to the fourth industrial revolution, started as a project that was part of the German government’s high-tech strategy.
The goal is to create smart networks that can autonomously control conditions throughout the value chain. Although we may still be at the beginning of this revolution, it is important to start planning for the future now. Especially sensible integration with the existing information technology infrastructure should not be taken lightly.
What is Industry 4.0?
Industry 4.0, characterized by digitization, merges physical environments with virtual ones to increase industrial competitiveness and trigger the country’s economic growth. Among its main benefits are:
- The incorporation of digital technology in industrial processes, which is capable of raising productivity by up to 25 percent.
- Reduce time to market by up to 50 percent.
- Increase the flexibility of production and its customization, as well as its quality.
- Industry 4.0 and technological solutions are for both SMEs and large companies, and more and more companies are discovering the benefits of this technological modernization.
Communication platforms
What is happening with the data that is collected from the machines? They need to be added to the central IT system to allow post-processing, useful visualization, and a basis for action by maintenance workers.
Monitoring things, in this case complex industrial machines, is not that different from monitoring network devices: what matters is getting relevant data that can be analyzed and put to a purpose.
That is, the precondition for a successful migration to smart manufacturing is the opening of production from its isolation and its integration with modern technologies.
When we talk about smart factories, we inevitably refer to machine-to-machine (M2M) communication. The goal of this concept is to collect data for processing and evaluation. The rapid development in the areas of IIoT (Industrial Internet of Things) and Industry 4.0 is driving this trend, which is why we see an increasing number of connected nodes in the industrial sector. In Germany, for example, a growth of 10% was obtained in 2019.
M2M communication is traditionally based on fieldbus protocol technology. Classic protocols such as profibus or modbus RTU, which have been used for many years, are well-developed and widely used in networks.
Well-known industrial ethernet protocols are ethernet/IP, modbus TCP, profinet, and ethercat. In Germany, industrial ethernet protocols have a market share of around 59%, with an annual growth rate of 20% compared to fieldbus protocols, with a market share of 35% and, for the first time, a 5 percent decrease.
The increasing spread of the 5G mobile communication standard will also speed up the development of M2M communication. The use of 5G removes the need for physical networks from the machines, which might have prevented system integrators from including them when they are located off-site. In addition, in the wireless sector (wlan, lpwan, bluetooth) a growth of 30% per year is observed and already represents 6% of the total market in Germany.
Increasing digitization demands the ability to be local in a global world, agile in a rapidly changing technology landscape, and open in an ecosystem of co-innovation. An enlarged enterprise, underpinned by digitization, is the solution to thriving in the digital economy.
RELATED BLOG POSTS
Discover Bridgeways’ Capabilities: Delivering Excellence Across Industries
Build Better with Bridgeways: Manufacturing Excellence and Community Impact
The Power of Contract Manufacturing
In today’s fast-paced and competitive business landscape, companies are constantly seeking ways to streamline their operations, reduce costs, and maintain high-quality standards.