by:
Maximizing Efficiency and Cost-Effectiveness through Outsourced Electronics Assembly
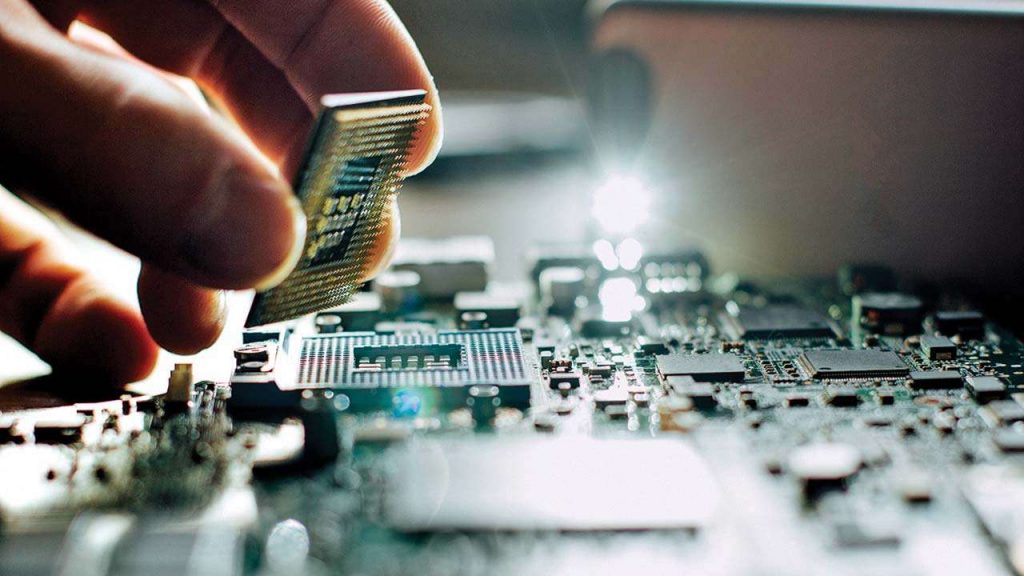
Outsourcing electronics assembly is the process of contracting with a third-party company, known as a contract manufacturer, to assemble electronic components into finished products. This can include anything from simple circuit boards to complex electronic systems and devices.
In outsourcing electronics assembly, the original equipment manufacturer (OEM) or the company that designs and develops the electronic product, will provide the contract manufacturer with all necessary specifications, design, and components.
The contract manufacturer will then assemble the electronic product according to the OEM’s specifications, using their own equipment, facilities and personnel.
The contract manufacturer will also be responsible for testing the product and making sure it meets the OEM’s quality standards. Once the product has passed the required quality checks and tests, it will be shipped back to the OEM for distribution and sale.
The Advantages of Outsourcing Electronics Assembly to Contract Manufacturers
Outsourcing electronic assembly to a contract manufacturing company can provide a number of benefits for businesses. These benefits include cost savings, access to specialized equipment and expertise, and increased flexibility and scalability.
One of the main benefits of outsourcing electronic assembly is cost savings. Contract manufacturing companies often have economies of scale that allow them to produce components and assemblies at a lower cost than a small business could achieve on its own.
In addition, contract manufacturers may have access to lower-cost materials and labor, which can further reduce production costs. Outsourcing electronic assembly can also help businesses avoid the costs of investing in expensive equipment and facilities, as well as the costs of maintaining and updating those assets over time.
Another benefit of outsourcing electronic assembly is access to specialized equipment and expertise. Contract manufacturing companies often have a wide range of equipment and capabilities that can be used to produce electronic assemblies. For example, they may have surface-mount technology (SMT) lines, automated optical inspection (AOI) systems, and other equipment that is not typically found in small businesses. They also often have highly skilled and experienced personnel who can work with complex electronic components and assemblies. Outsourcing electronic assembly can help businesses take advantage of these specialized resources without having to invest in them themselves.
Outsourcing electronic assembly can also increase flexibility and scalability for businesses. Contract manufacturing companies can often quickly ramp up or down production to meet the needs of their customers. This can be especially useful for businesses that have fluctuating demand for their products. In addition, outsourcing electronic assembly can allow businesses to focus on their core competencies and leave the production of electronic assemblies to the experts. This can help businesses become more efficient and competitive in the marketplace.
Another benefit of outsourcing electronic assembly is the ability to utilize the contract manufacturer’s quality control and testing capabilities. These companies typically have a wide range of quality control and testing equipment and procedures in place to ensure that the final product meets all relevant specifications and standards.
Moreover, outsourcing electronic assembly to a contract manufacturer can also provide businesses with greater access to global markets. Many contract manufacturers have facilities in different regions around the world, which can make it easier for businesses to sell their products in international markets.
Electronic Assembly Jobs that are Commonly Outsourced to Contract Manufacturers
There are a variety of electronic assembly jobs that are commonly outsourced to contract manufacturers. Some examples include:
- Surface-mount technology (SMT) assembly: This is the process of mounting electronic components onto a circuit board using surface-mount technology. SMT is a popular method for assembling electronic components because it is fast, accurate, and can handle a wide range of component sizes and shapes.
- Through-hole technology (THT) assembly: This is the process of inserting electronic components into holes drilled into a circuit board, and then soldering the component leads to the board. THT is often used for larger components or for those that need to be securely mounted to the board.
- Cable and harness assembly: This is the process of assembling wires, cables, and other electrical components into a finished product, such as a harness or cable assembly.
- Box-build assembly: This is the process of assembling all of the electronic components, including printed circuit boards, into a finished product, such as a control box or enclosure.
- Testing and quality control: This is the process of testing the assembled electronic product to ensure that it meets the OEM’s specifications and quality standards.
- Plastic injection molding: This is the process of injecting molten plastic into a mold to create a part that can be used in electronic assembly.
- Final product assembly: This is the final step of electronic assembly, where the final product is assembled, tested and packaged ready for shipment.
Depending on the complexity and the quantity of the electronic product, the OEM can choose one or multiple of the above mentioned jobs to outsource.
In conclusion, outsourcing electronic assembly to a contract manufacturing company can provide a number of benefits for businesses, including cost savings, access to specialized equipment and expertise, increased flexibility and scalability, and access to global markets. It can also help your business avoid the costs of investing in expensive equipment and facilities, as well as the costs of maintaining and updating those assets over time. Businesses can also utilize the contract manufacturer’s quality control and testing capabilities, which can help ensure that the final product meets all relevant specifications and standards.
RELATED BLOG POSTS
Unlocking Potential: The Transformative Power of Electrical Assembly
At Bridgeways, we believe in the transformative power of electrical assembly. It’s not just about connecting wires and components; it’s about unlocking the potential of innovation, efficiency, and progress. We’ll take a closer look at the role of electrical assembly in manufacturing and how Bridgeways is harnessing its power to drive positive change.